سیستم فلنج لوله
فلنج لولهکشی به فلنجی اطلاق میشود که برای لولهکشی در نصب خط لوله استفاده میشود و به فلنجهای ورودی و خروجی تجهیزات هنگام استفاده بر روی تجهیزات اشاره دارد. روی فلنج ها سوراخ هایی وجود دارد و پیچ ها باعث می شوند که دو فلنج محکم به هم متصل شوند. فلنج ها با واشر مهر و موم شده اند. فلنج به اتصال رزوه ای (اتصال رزوه ای) فلنج، فلنج جوشکاری و فلنج گیره تقسیم می شود. فلنج ها به صورت جفت، فلنج های سیمی برای خطوط لوله کم فشار و فلنج های جوشی برای فشارهای بیش از چهار کیلوگرم قابل استفاده هستند. یک واشر بین دو فلنج اضافه شده و سپس با پیچ و مهره سفت می شود. ضخامت فلنج ها با فشارهای مختلف متفاوت است و پیچ و مهره هایی که استفاده می کنند نیز متفاوت است. هنگامی که پمپ ها و شیرهای آب به خطوط لوله متصل می شوند، قسمت هایی از این تجهیزات و تجهیزات نیز به شکل فلنجی مربوطه در می آیند که به آن اتصالات فلنجی نیز می گویند. به کلیه قطعات اتصالی که در حاشیه دو صفحه توسط پیچ و مهره به هم متصل می شوند و همزمان بسته می شوند، به طور کلی «فلنج» می گویند، مانند اتصال لوله های تهویه. این نوع قطعات را می توان «قطعات فلنج» نامید. اما این اتصال تنها بخشی از تجهیزات است، مانند اتصال فلنج و پمپ آب، خوب نیست پمپ آب را «قطعات فلنج» بنامیم. کوچکترها مانند شیرآلات را می توان "قطعات فلنج" نامید.
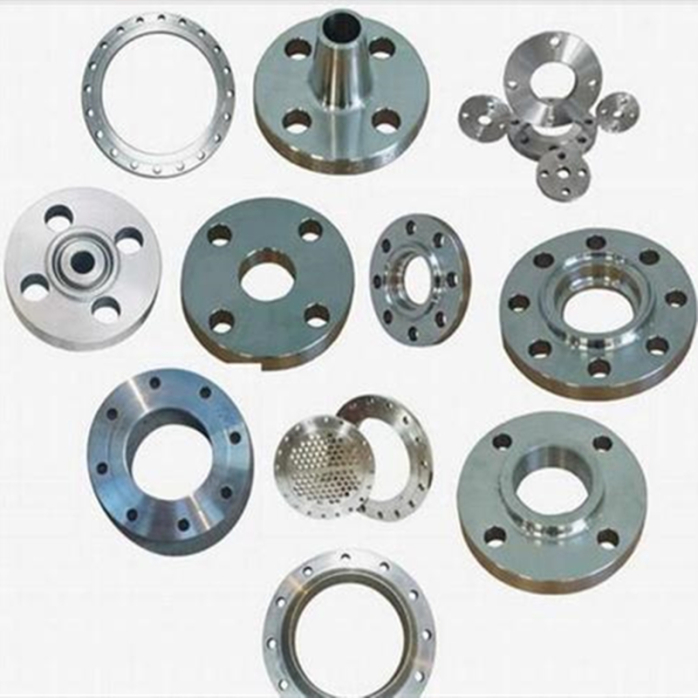
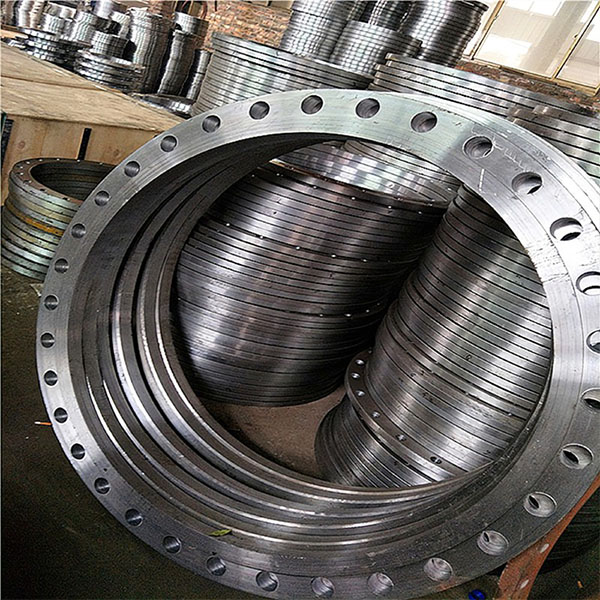
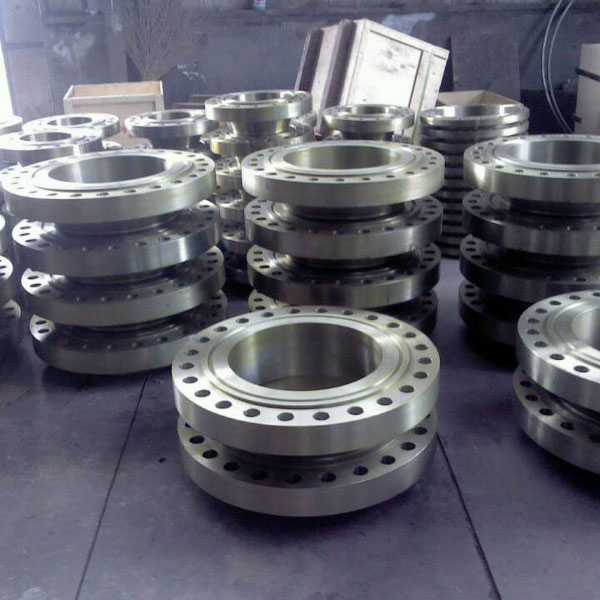
1. طبق استانداردهای صنعت صنایع شیمیایی (HG): فلنج انتگرال (IF)، فلنج رزوه ای (Th)، فلنج جوشکاری تخت صفحه (PL)، فلنج جوشکاری لب به لب گردن (WN)، فلنج جوشکاری صاف گردن (SO)، سوکت فلنج جوش (SW)، فلنج شل حلقه جوش لب به لب (PJ/SE)، فلنج شل حلقه جوش تخت (PJ/RJ)، پوشش فلنج آستر (BL(S))، پوشش فلنج (BL).
2. طبق استاندارد صنعت پتروشیمی (SH): فلنج رزوه ای (PT)، فلنج جوش لب به لب (WN)، فلنج جوشکاری تخت (SO)، فلنج جوش سوکت (SW)، فلنج شل (LJ)، پوشش فلنج (نمایش داده نشده است). ).
3. با توجه به استانداردهای صنعت ماشین آلات (JB): فلنج انتگرال، فلنج جوش لب به لب، فلنج جوشکاری تخت صفحه، فلنج شل صفحه حلقه جوش لب به لب، فلنج شل صفحه حلقه حلقه، فلنج شل صفحه حلقه فلنج فلنج فلنج، پوشش فلنج.
4. مطابق با استانداردهای ملی (GB): فلنج های یکپارچه، فلنج های رزوه ای، فلنج های جوش لب به لب، فلنج های جوشکاری صاف گردن، فلنج های جوشکاری سوکت گردن، فلنج های شل حلقه حلقه جوش لب به لب، فلنج های صاف صفحه فلنج های جوشکاری، فلنج های جوش لب به لب، فلنج های جوش لب به لب ، فلنج های شل صفحه حلقه جوش تخت، فلنج های شل صفحه حلقه فلنج، پوشش های فلنج.
WCB (فولاد کربن)، LCB (فولاد کربن با دمای پایین)، LC3 (3.5٪ فولاد نیکل)، WC5 (1.25٪ کروم 0.5٪ فولاد مولیبدن)، WC9 (2.25٪ کروم)، C5 (5٪ کروم 0.5٪ مولیبدن)، C12 (9٪ کروم و 1٪ مولیبدن)، CA6NM (4 (فولاد کروم 12 درصد)، CA15 (4) (12 درصد کروم)، CF8M (فولاد ضد زنگ 316)، CF8C (فولاد ضد زنگ 347)، CF8 (فولاد ضد زنگ 304)، فولاد ضد زنگ CF3 (304 لیتر)، فولاد ضد زنگ CF3M (316 لیتر) فولاد)، CN7M (فولاد آلیاژی)، M35-1 (Monel)، N7M (Haast نیکل آلیاژ B)، CW6M (Hasta نیکل آلیاژ C)، CY40 (Inconel) صبر کنید.
فرآیند تولید به طور عمده به چهار نوع تقسیم می شود: آهنگری، ریخته گری، برش و نورد.
(1) فلنج ریخته گری و فلنج آهنگری
فلنج ریخته گری دارای شکل و اندازه دقیق، حجم پردازش کوچک و هزینه کم است، اما دارای عیوب ریخته گری (منافذ، ترک ها، آخال ها) است. ساختار داخلی ریخته گری از نظر خط جریان ضعیف است (اگر قسمت برش باشد، خط جریان بدتر است).
فلنج های فورج شده معمولاً دارای کربن کمتری نسبت به فلنج های ریخته گری هستند و به راحتی زنگ نمی زنند. فورجینگ ها روان هستند، ساختار متراکم تری دارند و خواص مکانیکی بهتری نسبت به فلنج های ریخته گری دارند.
فرآیند آهنگری نامناسب همچنین باعث ایجاد دانه های کریستالی بزرگ یا ناهموار، ترک های سخت شده و هزینه آهنگری بالاتر از فلنج های ریخته گری می شود.
آهنگری ها نسبت به ریخته گری می توانند نیروهای برشی و کششی بالاتری را تحمل کنند.
مزیت ریخته گری این است که آنها می توانند اشکال پیچیده تر و هزینه کمتری تولید کنند.
مزیت آهنگری این است که ساختار داخلی یکنواخت است و هیچ عیب مضری مانند منافذ و آخال در ریخته گری وجود ندارد.
از فرآیند تولید، تفاوت بین فلنج ریخته گری و فلنج آهنگری متفاوت است. مثلا فلنج گریز از مرکز نوعی فلنج ریخته گری است.
فلنج های گریز از مرکز متعلق به روش ریخته گری دقیق برای تولید فلنج هستند. در مقایسه با ریخته گری شن و ماسه معمولی، ساختار این نوع ریخته گری بسیار ظریف تر است و کیفیت آن بسیار بهبود یافته است. مستعد مشکلاتی مانند شل شدن ساختار، منافذ و تراخم نیست.
اول از همه، ما باید نحوه تولید فلنج گریز از مرکز، روش فرآیند و محصول ریختهگری گریز از مرکز را برای ساخت فلنج جوشکاری مسطح بدانیم، که مشخصه آن این است که محصول طی مراحل فرآیند زیر پردازش میشود:
① فولاد مواد خام انتخاب شده را برای ذوب در یک کوره الکتریکی فرکانس متوسط قرار دهید تا دمای فولاد مذاب به 1600-1700 درجه سانتیگراد برسد.
② قالب فلزی را تا 800-900 ℃ برای حفظ دمای ثابت از قبل گرم کنید.
③ سانتریفیوژ را راه اندازی کنید و فولاد مذاب را در مرحله ① پس از پیش گرم کردن در مرحله ② در قالب فلزی بریزید.
④ ریخته گری به طور طبیعی تا 800-900 ℃ خنک می شود و به مدت 1-10 دقیقه نگهداری می شود.
⑤ با آب تا دمای معمولی خنک کنید، قالب را خارج کنید و قالب را خارج کنید.